Bioactive glass, smartphone cover glass, solid-state glass batteries—these cutting-edge materials and innovative applications implicitly announce “Welcome to The Age of Glass!”1
Glass is certainly not a new material—it has helped advance the quality of life for millennia in the forms of containers, windows, and adornments. But our ability to design and produce specialty glasses for applications spanning healthcare, communications, and astronomy, among others, has led us into an epoch where glass plays an integral role in transforming society for the better.
Novel glass compositions, such as LionGlass (see “LionGlass recycling: Preparing for the industrial transition” in this issue), are one core component of advancing the Glass Age. But so, too, is the development of state-of-the-art processing techniques and technologies, which can help improve the carbon footprint and material properties of existing glass compositions.
Chemical strengthening, or ion exchange (IOX), is one processing approach that can alter the mechanical, optical, and electrical properties of a formed glass. While the technique has largely been applied to specialty glass compositions (more on that below), this article considers the potential of using IOX to improve the production of commercial-grade soda-lime-silica (SLS) glasses and identifies factors that could either accelerate or slow future advances.
Kinetics and mechanics of the IOX process
IOX strengthening of glass results from the interdiffusion-controlled removal of a small radius ion (typically sodium, Na+, radius ~0.10 nm) and replacement with a larger ion (typically potassium, K+, radius ~0.12 nm). This exchange is achieved by placing the glass in an IOX bath containing a source of K+ ions, usually liquid KNO3.2
When the potassium ion comes to occupy the sodium ion site, the site must expand to accommodate the larger ion. Because the glass is a solid during this process, it cannot easily change structure, so expansion of the smaller ion site causes compression of the structure between the two ions. The equation modeling this compressive stress can be seen in Figure 1.3 Compressive stresses as high as 1,200 MPa have been obtained in aluminosilicate glasses and as high as 800 MPa in SLS glasses.
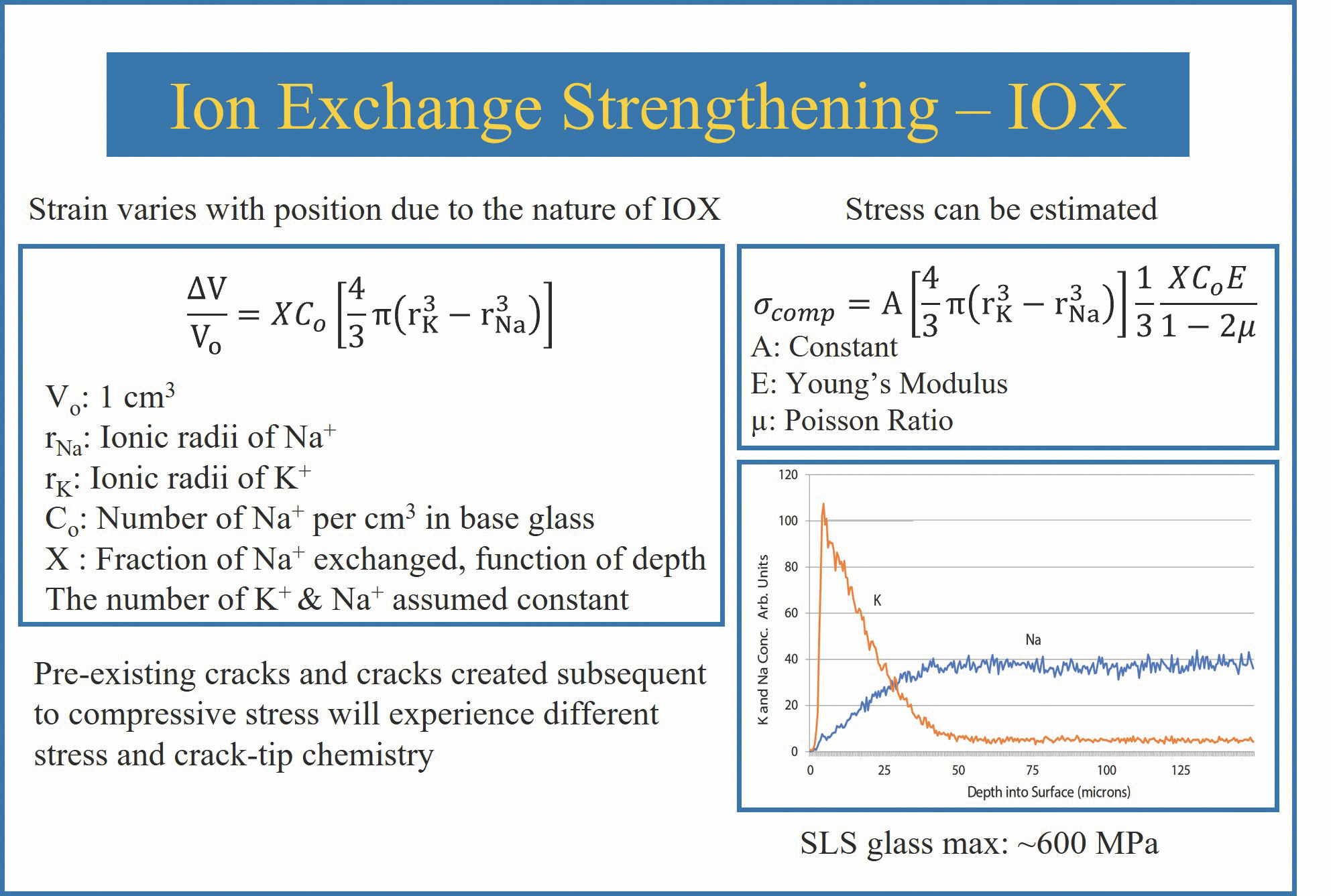
Figure 1. (Upper left) General equation for strain due to IOX. (Upper right) Equation for surface compressive stress due to IOX. The correction factor, termed “A,” recognizes that the sites occupied by the two ions may not be spherical. (Bottom right) Example maximum diffusion distance and relative concentration of sodium and potassium ions in IOX SLS glass, determined using energy dispersive X-ray spectroscopy. Adapted from Reference 3. Credit: Jacob Kaspryk
Because the IOX process puts significant strain on the glass, IOX is best carried out at least 50°C below the glass’s strain point (i.e., the temperature where the viscosity of the glass is 1013.5 Pa•s). If the glass was processed at the strain point, it would take about four hours to fully relax any IOX-induced stress. The strain point for commercial SLS glasses is near 500–510°C, whereas alkali aluminosilicates are much higher, in the range of 570–650°C.
The depth of layer (DOL), i.e., the depth from the surface at which the ion exchange process occurs, can be determined using Equation 1. It relates DOL to a single diffusion coefficient D, which describes the effective diffusion coefficients of the two mobile ions, and the time dependence of the penetration as described by the root mean square penetration distance, drms. In general, a deeper DOL leads to improved mechanical properties and fracture resistance.
Equation 1
DOL =√3 drms, where drms = (2D•t)0.5
IOX successes with non-SLS glasses
As noted in the introduction, IOX to date has largely been applied to specialty glass compositions. Cover glasses such as DragonTail (Asahi, Japan), Gorilla Glass (Corning Inc., U.S.), and Panda Glass (Tungshu Group, China) are examples of IOX sodium aluminosilicate glasses, while the cover glass Xensation (Schott, Germany) is an example of an IOX lithium boroaluminosilicate glass.
The success of these products lies with the ways composition affects structure. Specifically, two important changes occur when Al2O3 and/or B2O3 are added to the base sodium silicate composition.4 First, the weak NBO bonds are replaced by much stronger Al–O–Si or B–O–Si bonds. Typically, the aluminum (Al3+) or boron (B3+) ions share four oxygens, each of which form four strong “bridging” oxygens (Al–O–Si). Second, following IOX, alkali ions no longer bond to nonbridging oxygen ions. Instead, they bond less strongly to negatively charged structures associated with (Al–O4)– tetrahedra, which leads to increased mobility of the alkali ions. Thanks to these two changes, the IOX cover glasses demonstrate increased scratch and drop resistance.
The one major downside of IOX specialty glasses is their more energy-intensive manufacturing process. The reduced NBO content in aluminosilicate and boroaluminosilicate glasses causes these compositions to have increased viscosities, which requires the glass to be processed at noticeably higher temperatures—which translates to much higher production costs.
For example, melting temperatures for Gorilla Glass, DragonTrail, and Xensation are roughly 100–200°C higher than for SLS glasses. Gorilla Glass windshields for a Jeep Wrangler can reach $1,000,5 for example, about three times more expensive than a conventional SLS glass windshield.
Despite the increased production costs, superior properties such as scratch resistance and compressive strength reaching 1,200 MPa justify the expenditure for certain applications.
Challenges with IOX processing of SLS glasses
The sale of and market for IOX glass products have grown since Gorilla Glass’s debut in the original iPhone in 2007.6 However, IOX and other specialty glass compositions, such as fiberglass, still only account for approximately 10% of the global glass market—the other 90% is taken up by SLS glasses in the form of float glass and containers.
There are surprisingly few differences in SLS composition across different products and companies, as shown in Table 1.3,7 The major compositional difference between float glass and container glass is a lower MgO content compensated for by increased CaO in container glass.
Obviously, there are cost benefits to using a single, base glass composition to mass produce multiple products. But the current base SLS composition and form factor presents some challenges to processing SLS glass using chemical strengthening.
Modern float (“flat”) glass is made by floating molten glass on a bath of molten tin. As the name “flat” implies, float glass factories produce limited shape variations, with the major difference being glass thickness. The process can produce plates as thin as 0.4 mm and up to 25 mm thickness, allowing a wide range of products to be produced using the same composition.
Some factories can produce 800–1,200 tons per day of SLS glass. Different lengths and widths can be cut from the standardized sheets, and different colors are obtained in-house by performing post-forming surface treatments. Other post-forming treatments, such as thermal tempering or IOX processing, take place in secondary manufacturing facilities.
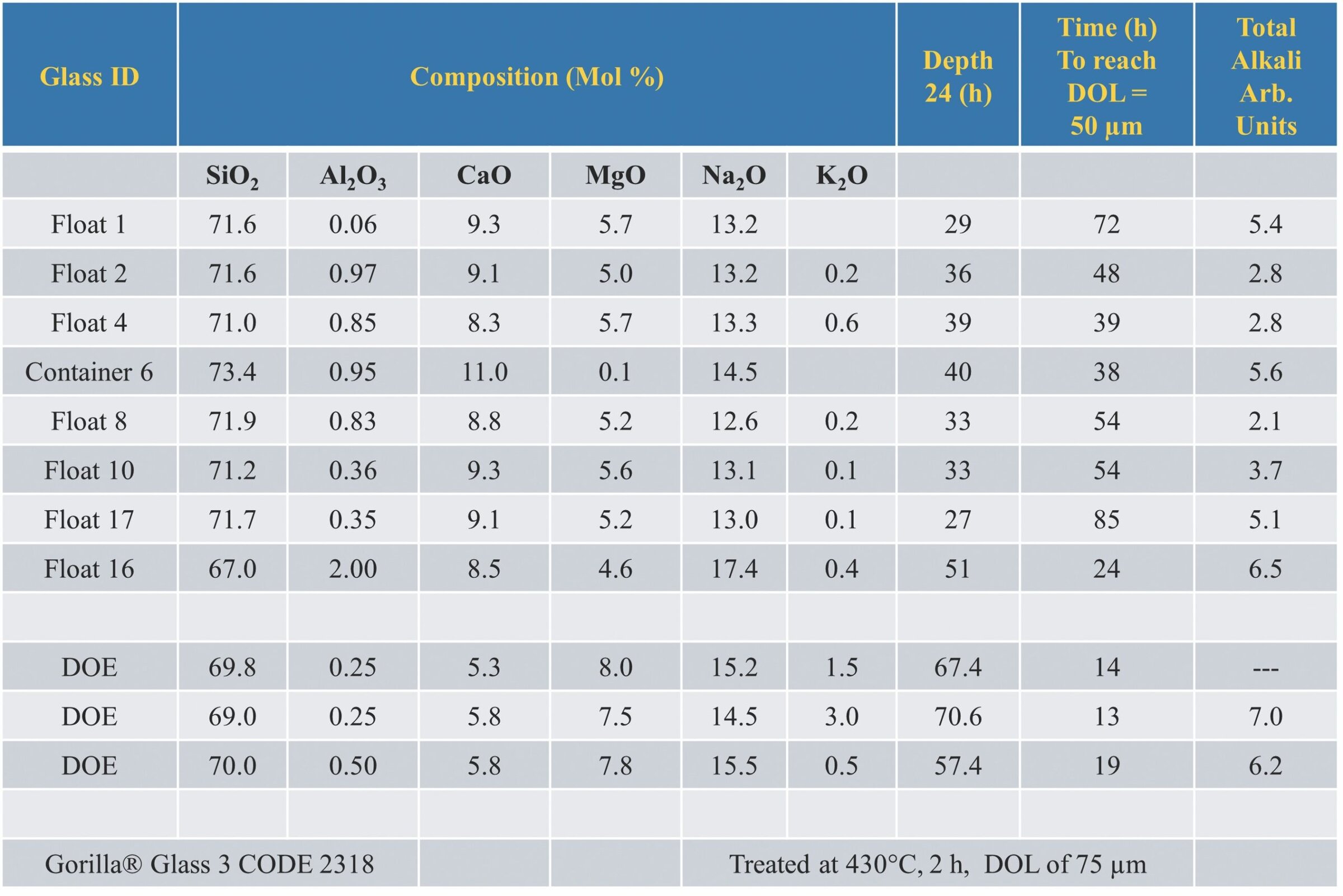
Table 1. Composition and properties of some commercial and experimental SLS glasses. Includes maximum depth of layer (DOL) for a 24-hour ion exchange period at 450°C; the time required to achieve a 50 µm DOL; and chemical durability as measured by the amount of sodium leached per gram of glass in one hour. For float samples, the DOL was measured on the air side of the floating glass because glass on the molten tin side exhibits a lower diffusion rate that varies with thickness due to the different contact times of the glass and molten tin. Adapted from Reference 3. Credit: Jacob Kaspryk
As stated earlier, a deeper DOL during IOX processing typically leads to greater resistance to cracking and fracture. But as seen in Table 1, the DOL for all commercial SLS compositions is extremely low, ranging from 24–51 µm after a 24-hour treatment at 450°C. In contrast, Gorilla Glass (last line in Table 1) develops a DOL of more than 50 µm following treatment for two hours at 430°C.
Achieving a DOL of 50 µm in commercial SLS compositions requires exposure times between 24–85 hours. And even then, surface compression strengths of 800 MPa or more cannot be reached consistently.
Because most SLS glass applications do not require high strength, some may assume IOX processing of SLS glass is not a worthwhile pursuit. However, there is one big advantage to subjecting SLS glass to IOX processing: lightweighting.
Lightweighting involves making an object weigh less without compromising its mechanical properties or performance. Successful lightweighting reduces raw material requirements, which translates to reduced manufacturing and shipping costs, among other benefits.
High-volume markets for lightweight glass products include energy (e.g., solar panels) and transportation (e.g., windshields for cars, aircraft, and boats). In the former case, reducing solar panel thickness from 3 mm to 2 mm would reduce its weight by more than 30%, making installation easier and reducing the need for structural reinforcement. In the latter case, a 10% reduction in vehicle weight can improve fuel economy by 6–8%.8
Lightweighting also has benefits in commercial and residential construction. The U.S. Department of Energy estimates that drafts, leaks, and inefficiencies cost U.S. households at least $25 billion dollars each year.9 By lightweighting glass windows, new three- and four-pane windows can be fabricated that are comparable in thickness to typical double-pane windows but with highly improved insulation capabilities.10
Both thermal and chemical processing treatments can be used for lightweighting. However, thermal tempering becomes dramatically less effective at glass thicknesses less than 3 mm, while IOX maintains its strengthening ability—thus making it the preferred approach for certain energy and construction applications.
IOX specialty glasses are starting to be used for these lightweighting applications, for example, the Gorilla Glass automotive windshields mentioned earlier. But if SLS glasses could achieve DOLs of 50 µm within exposure times only 20–30% longer than aluminosilicates—rather than the current 10 times or more—they could offer similar benefits at a more affordable cost due to the lower melting temperature. Thus, there is a strong incentive to overcome the challenges with IOX processing of SLS glasses.
Current successes and possible solutions to IOX SLS glass processing
In Table 1, commercial composition Float 16 came close to achieving the threshold 50 µm DOL within an exposure time only 20–30% longer than aluminosilicates. However, that composition is no longer produced.
Some modified SLS compositions have reached the threshold 50 µm DOL in less than 20 hours. For example, the three experimental compositions created as part of a U.S. Department of Energy project (labeled DOE in Table 1) achieved the required threshold in 14, 13, and 19 hours, respectively.
We also achieved the desired threshold in experiments conducted at Alfred University.11 As seen in Table 2,3 composition A (X = 4, 6, or 8) achieved the threshold 50 µm DOL when processed for 16 hours at 450°C. (Additional interesting findings in the Alfred experiment are detailed in the sidebar “The mixed alkali effect in IOX SLS glass processing.”)
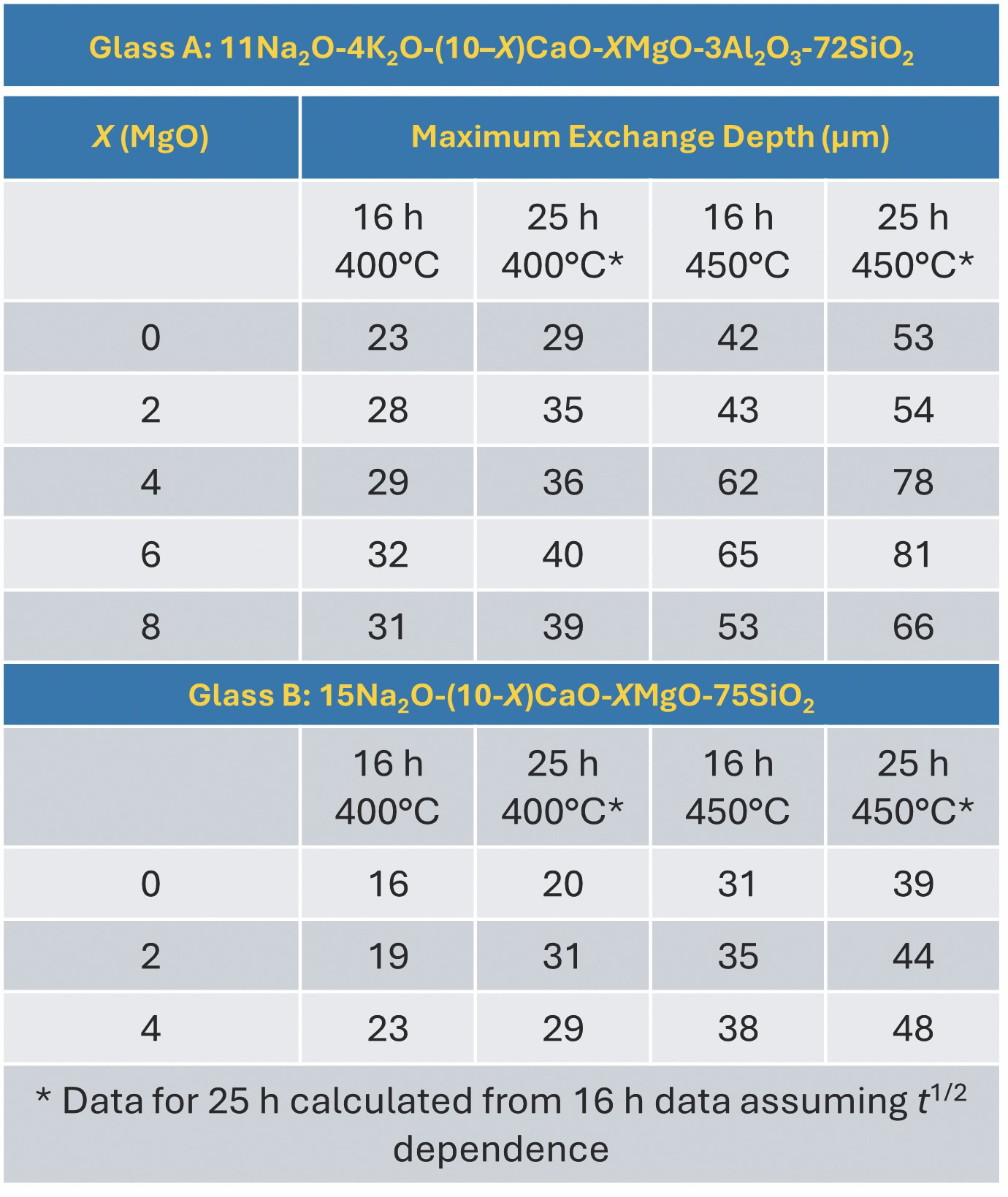
Table 2. Depth of layer for two compositions of MgO-containing SLS glasses. Adapted from Reference 3. Credit: Jacob Kaspryk
Though the experimental glasses (DOE compositions in Table 1 and composition A in Table 2) achieved sufficiently deep DOLs in much shorter times, the successful compositions are noticeably different from commercial SLS glasses. Because mechanical–property relationships in IOX glass surfaces can be quite complicated, tweaking compositions to provide improvement in one property may not benefit other properties.
For example, Figure 2 shows the DOL versus compressive strength for some standard and IOX SLS glasses based on composition A in Table 2.3,11 While IOX processing generally results in higher compressive strength, surprisingly, initial four-point bending tests found the commercial float glass composition had the highest compressive strength despite having the lowest DOL value (25 µm). The commercial float glass composition’s compressive strength did decrease dramatically after abrasion, however, and came in last upon retesting.
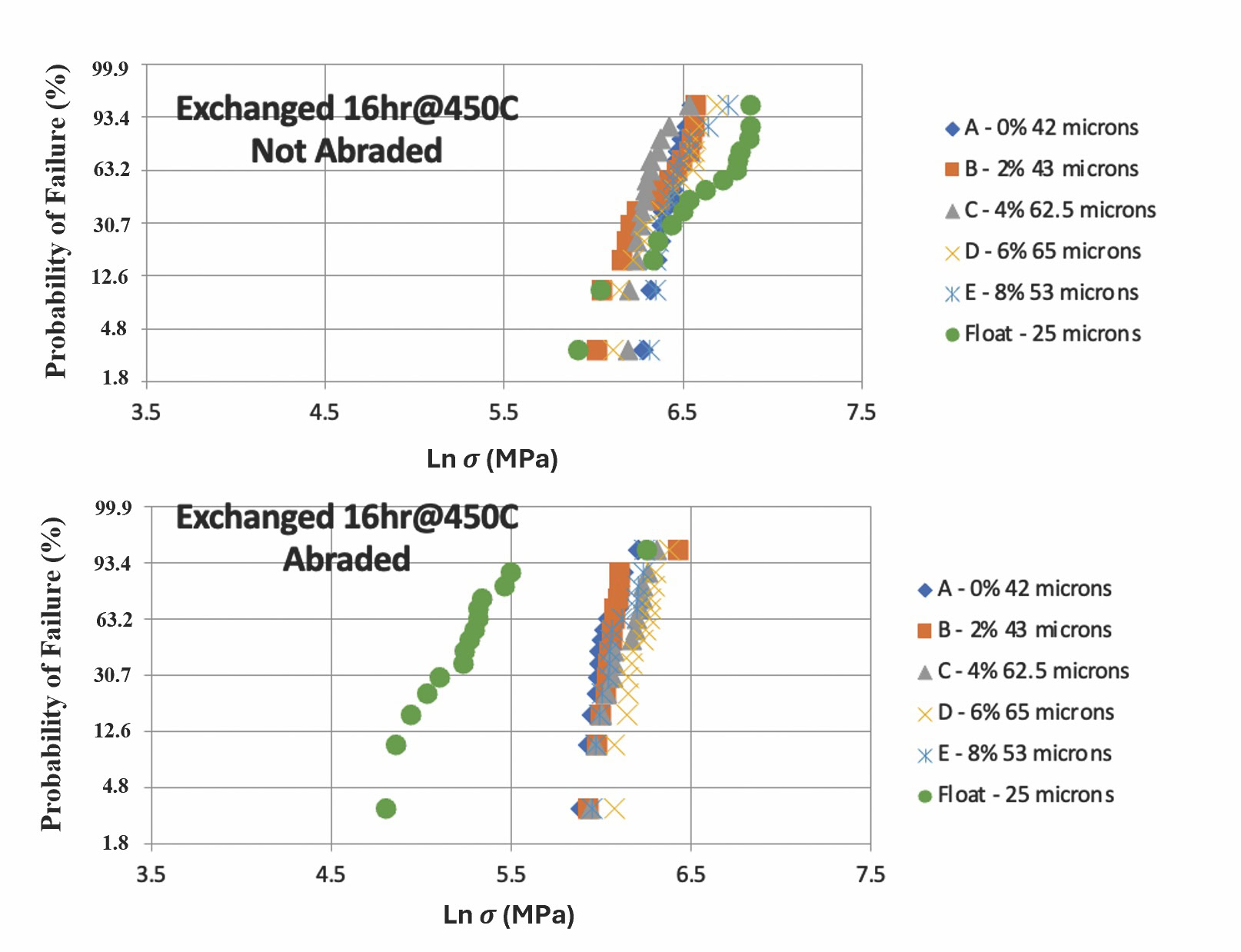
Figure 2. Weibull statistics (probability of failure) versus load. Combined strengthening effects using the mixed alkali glass with 11 mol% Na2O and 4 mol% K2O and substitution of up to 8 mol% Mg2+ for Ca2+ samples of composition A from Table 2. An increase in the Mg2+ concentration caused a rapid increase in DOL and a corresponding increase in abrasion resistance. The commercial SLS glass (green data points) showed excellent strengthening (top curves) but poor abrasion resistance due to the low DOL. Other studies at Alfred suggest that DOL levels of 40 µm or more are required to avoid large strength decreases by impact or scratching. Adapted from Reference 3. Credit: Jacob Kaspryk
Because of the different properties between standard SLS glass and IOX SLS glass, manufacturers would need to process IOX SLS glass separately from the standard SLS glass to avoid contamination. But unfortunately, constructing a new facility for IOX SLS glass would be a costly addition that could only be justified by a large market for IOX SLS glass.
Instead of an entirely new facility, it may be possible to adopt a production strategy used for colored container glasses: multiple forehearths on a single melter. Currently, float glass is produced using a single melter and a single forehearth, i.e., a reservoir for holding the molten material before it is poured or withdrawn for further processing. In contrast, colored container glass production involves directing the molten material into multiple forehearths, which permits changes to the glass in small batches rather than committing the entire melt to a single color.
If this multi-forehearth setup was used for float glass, it would permit changes in the bulk composition without committing the entire melt to the modified SLS composition. Conversations with people familiar with coloring forehearths suggest that compositional modifications on the order of 5–8% would be “easy” and that larger changes might be possible. A lecture on the potential of this multi-forehearth approach was given at the 84th Conference on Glass Problems,12 and the presentation is available upon request.
Such an approach to flat glass production may seem a bit far out, but as the market demand for lightweighting SLS glass products grows, it will be essential to consider this and other approaches to making IOX SLS processing economically feasible. Below are two more approaches that could help in realizing this market opportunity.
Suggestion 1: Noncompositional methods for accelerated IOX processes
Methods that do not require significant compositional modifications to achieve accelerated IOX processing times are important to consider. Even simple approaches, such as using a programed nonisothermal IOX process,13 could allow rapid diffusion by starting at a high temperature (450–475°C) followed by programed cooling to avoid relaxation effects.
Ultrasound-assisted diffusion could also help increase diffusion rates.14,15 Theory indicates that the probability of ion diffusion increases more in the direction of increasing tension than it decreases in the direction of increased compression. The effect is small for a given cycle, but at high frequencies, the effect will be magnified.
There is, however, a possible negative effect—the extra energy of the vibrations might cause relaxation at lower temperatures than predicted, resulting in a loss of the stress-induced diffusion. It is known that both effects can occur, but the importance of the effects and the temperature dependences are not known. These factors need to be investigated.
Suggestion 2: Effects of preexisting flaws in IOX glass
Most discussions regarding IOX processing focus on improving the glass to avoid scratches and impact damage. But what if it is too late? What if the glass was scratched or damaged during removal from the production line or in transit to the secondary manufacturing facility?
While some surface flaws cannot be strengthened by IOX, such as half-penny cracks caused by Vickers indentation, others can benefit from the IOX process. For example, some surface crack geometries are such that the IOX bath is drawn into the crack by capillary action and by interdiffusion along the remaining distance to the crack tip. Figure 3 shows a few cases in which the ion-exchange liquid, doped with AgNO3 to increase visibility under scanning electron microscopy, shows penetrations of as much as 100 µm.16,17 As the IOX process progresses, the crack opening may narrow due to the IOX-induced glass expansion.
There are still a lot of unknowns regarding how preexisting flaws affect the IOX process. Studies that provide more information would be worthwhile.
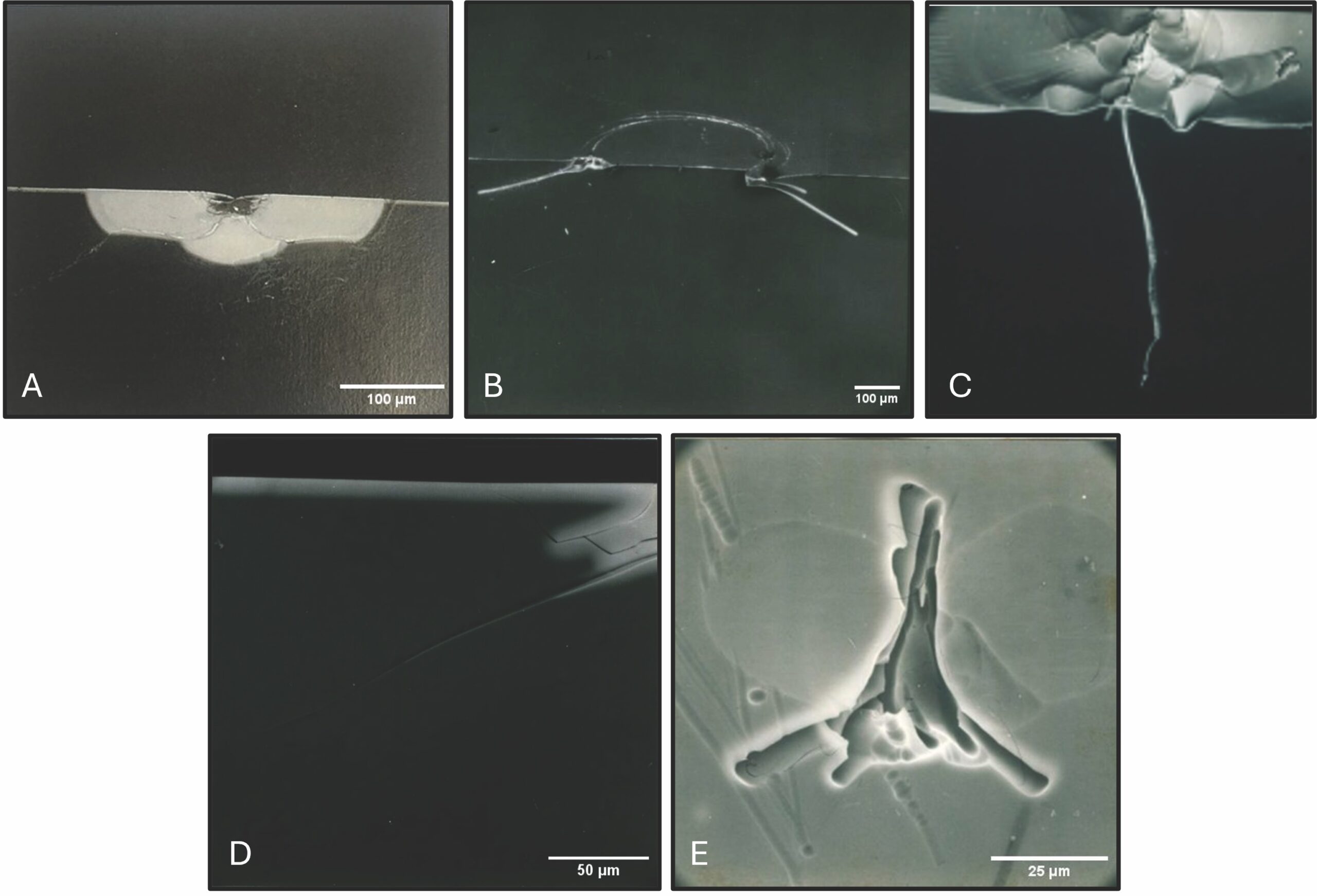
Figure 3. A–D: Various surface flaws in SLS glass after IOX treatment in AgNO3. (A) Vickers indentation, 2 kg; (B,D) blunt indentation, 60 kg; (C) scratch, 200x magnification. White highlighted part is indicative of the presence of silver via scanning electron microscopy backscatter imagery of the cross section. E: Top-down view of acid-etched SLS to demonstrate the complexity of surface flaw geometry. The flaw was caused by dropping a 1-mm-diameter silicon carbide ball on the glass. Republished with permission from References 16 and 17. Credit: A–D: Ruth17; E: Vitch16
Ultimately, there is much to be learned—and, conversely, much opportunity to be lost—when it comes to IOX processing of SLS glass. By engaging researchers in academia, government, and industry, we can successfully identify factors that could either accelerate or slow IOX SLS glass advances and ideally open the door to the commercial success of new chemically strengthened glass products. We can then introduce and welcome everyone to the new (and more advanced) Glass Age.
Read more: The mixed alkali effect in IOX SLS glass processing
Cite this article
W. C. LaCourse, J. Kaspryk, and B. J. A. Moulton, “Prospects for ion-exchange processing of commercial soda-lime-silica glasses,” Am. Ceram. Soc. Bull. 2025, 104(4): 22–27.
About the Author(s)
William LaCourse is emeritus professor of glass science, Jacob Kaspryk is a graduate student in glass science, and Benjamin J. A. Moulton is assistant professor of glass science and engineering at Alfred University in New York. Contact LaCourse at lacourse@alfred.edu.
Issue
Category
- Glass and optical materials
- Manufacturing
Article References
1J. Ballato et al., “Affirmation of The Age of Glass,” Am. Ceram. Soc. Bull. 2024, 103(9): 4–5.
2G. Macrelli, J. C. Mauro, and A. K. Varshneya, “Coupling of diffusion and chemical stress: The case of ion exchange in glass,” Journal of the American Ceramic Society 2021, 104(11): 5599–5613.
3W. C. LaCourse, “Design of SLS compositions for accelerated chemical strengthening,” Ceramic Engineering and Science Proceedings 2018, 39: 181–189.
4K. J. Rao, Structural Chemistry of Glasses. Elsevier Science: New York, 2002. p. 568
5“Corning Gorilla Glass for automotive exteriors,” Corning. Accessed 3 April 2025.
6S. Berneschi, G. C. Righini, and S. Pelli, “Towards a glass new world: The role of ion-exchange in modern technology,” Applied Sciences 2021, 11(10): 4610-4646.
7C. W. Sinton, W. C. LaCourse, M. J. O’Connell, “Variations in K+–Na+ ion exchange depth in commercial and experimental float glass compositions,” Materials Research Bulletin 1999, 34(14–15): 2351–2359.
8“Lightweight materials for cars and trucks,” U.S. Department of Energy. Accessed 1 April 2025.
9“Why energy efficiency matters,” U.S. Department of Energy. Accessed 3 April 2025.
10C. Mims, “A piece of glass thinner than a credit card could solve America’s $25 billion energy problem,” The Wall Street Journal. Published 21 March 2025. Accessed 3 April 2025.
11M. J. O’Connell, “The effects of MgO replacement of CaO on the ion exchange behavior.” M.S. thesis, Alfred University, 1998. Supervised by William C. LaCourse.
12W. C. LaCourse, D. Swiler, M. Choudhary, A. Cormack, and S. K. Sundaram, “Accelerated melting and homogenization for single melter and multi-forehearth processes.” Presented at the 84th Conference on Glass Problems, November 2023, Columbus, Ohio. Contact LaCourse at lacourse@alfred.edu for a shortened version of this material.
13J. Shen and D. J. Green, “Variable temperature ion-exchanged engineered stress profile glasses,” Journal of the American Ceramic Society 2003, 86(11), 1979–1981.
14H. Wang, “Sonic strengthening effect on soda-lime silicate glass,” M.S. thesis, Alfred University, 1991. Supervised by William C. LaCourse.
15V. Geyer, “Ultrasonic-assisted ion exchange in commercial float glass,” M.S. thesis, Alfred University, 1994. Supervised by William C. LaCourse.
16S. M. Vitch, “The effect of flaw origin on the ion-exchange strengthening of glass,” M.S. thesis, Alfred University, 1988. Supervised by William C. LaCourse.
17K. Ruth, “Direct observation of ion exchange in flaw damaged glasses,” M.S. thesis, Alfred University, 1991. Supervised by William C. LaCourse.
Related Articles
Bulletin Features
How DOE’s no-cost technical assistance resources support today’s glass and ceramics manufacturers
The U.S. Department of Energy (DOE) recognizes that an efficient and robust domestic manufacturing sector is essential for creating high-paying American jobs and ensuring a prosperous economy. To that end, DOE’s Advanced Manufacturing Office (AMO) is committed to fostering a strong, diverse base of American manufacturers that lead the world…
Bulletin Features
Solid oxide fuel cell technology for the future
According to the U.S. Department of Energy’s Energy Information Administration (EIA), world energy consumption will increase to about 740 quadrillion Btu in 2040, rising 28% between 2015 and 2040.1 The EIA projects that increases in consumption will affect all energy sources—fossil (petroleum and other liquids, natural gas), renewables (solar, wind,…
Bulletin Features
Flow batteries and energy storage— a new market for ceramics
Redox flow batteries belong to a large and growing group of devices designed for energy storage applications. Although their origins trace back to a zinc/chlorine flow battery used to power an airship in 1884,1 rapid, systematic growth in the redox flow battery market has only been apparent within the past…